The challenges of becoming a high-tech paper packaging supplier for the F&B industry, specifically the dairy industry, are significant.
In April 2024, Nutifood introduced a new product line for Varna Colostrum, a premium nutritional milk for adults, offering paper boxes in addition to the plastic bottles previously used.
Mr. Mai Thanh Viet, Deputy General Director of Nutifood, explained that the DomeMini bottle-shaped paper box design by SIG is very aesthetic and convenient, with the DomeMiniCap lid located in the center for easy opening and closing during product usage and storage throughout the day.
To achieve maximum recycling efficiency, SIG’s DomeMini bottle-shaped paper boxes are made from FSCâ„¢-certified cardboard from renewable wood sources, and the production process consumes 100% renewable electricity. The compact design also helps save storage space.
Additionally, SIG’s DomeMini 12 aseptic filling system offers a filling capacity of 12,000 bottles per hour for seven volume levels ranging from 180-350ml, and it allows for volume changes in just 15 minutes. This ensures maximum efficiency and flexibility, guaranteeing superior investment returns for beverage manufacturers.
Nutifood’s decision to adopt SIG’s packaging and filling system goes beyond simply replacing plastic bottles with paper boxes for Varna Colostrum. It involves a significant investment in machinery, with each filling line estimated to cost millions of USD. With seven volume levels, Nutifood can utilize this system not just for the Varna brand but also for other milk and beverage brands under their umbrella.
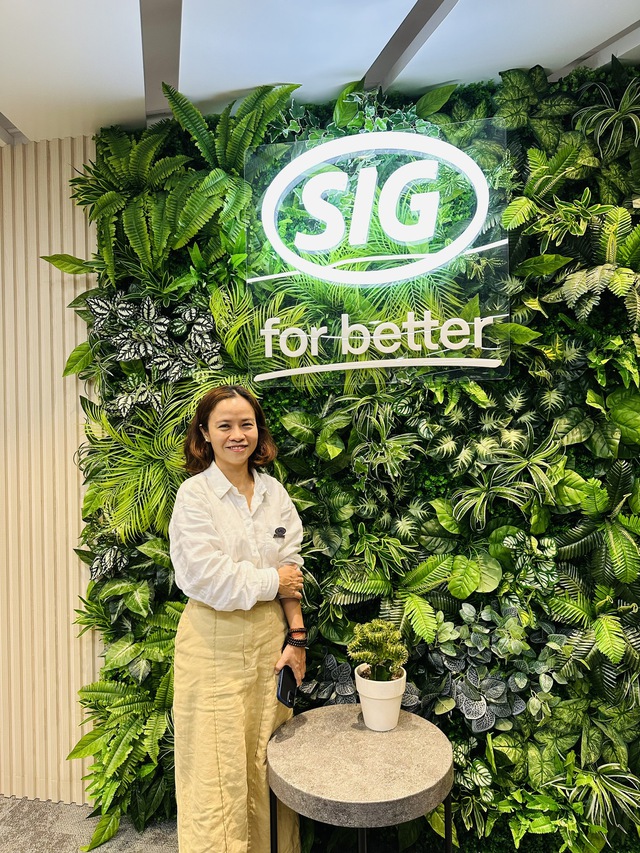
Ms. Vo Xuan Minh Kha, Country Manager of SIG Vietnam
According to Ms. Vo Xuan Minh Kha, Country Manager of SIG Vietnam, the new filling system has made Varna milk more competitive and accessible to a wider range of customers, now offered at VND 25,000/box instead of VND 35,000/bottle.
The industry of supplying paper packaging for dairy and beverage products requires advanced technology, machinery, and material science expertise accumulated over decades, which is a challenge for young industrial countries like Vietnam.
For instance, the technology behind packaging that combines paper, plastic, and aluminum for the dairy and beverage industry is a groundbreaking human invention that has been constantly improved to meet evolving consumer demands. SIG, with its over 170 years of history, has now even eliminated the aluminum layer, ensuring the same milk quality with just paper and a thin plastic layer.
Currently, no Vietnamese paper packaging company can produce the three-material boxes like Tetra Pak or SIG, let alone achieve sterilization with only two materials or manufacture filling systems.
In the Vietnamese market, Tetra Pak and SIG, both European companies that entered the market in the early 2000s, dominate this field. Tetra Pak is more widely known due to its local factory with a total investment of USD 217 million since 2019. In February 2024, Tetra Pak announced the closure of its packaging material factory in Jurong, Singapore, and its office in Singapore, which employed 300 people. Tetra Pak also has a factory and a technical training center for customers in Thailand.
On the other hand, SIG does not have a factory in Vietnam because it already has a large factory in Thailand, established in the Rayong Industrial Zone since 1998, spanning 109,600m2. This complex serves SIG’s customers in the Asia-Pacific, South Asia, and especially Southeast Asia, Australia, Japan, and India.
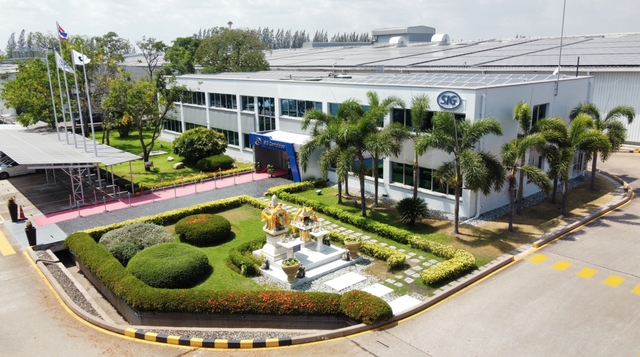
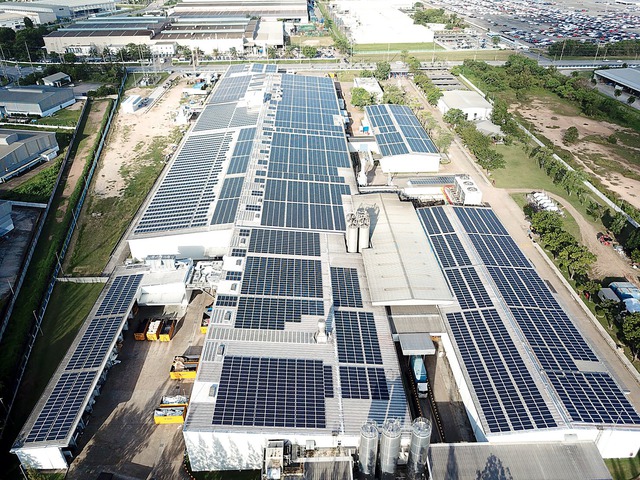
SIG’s factory in Thailand.
In Vietnam, SIG has approximately 50 employees, half of whom are engineers working at partner factories. According to the CEO of SIG Vietnam, the company’s responsibility does not end with selling the filling lines; SIG also provides annual maintenance and proposes upgrades or replacements every five to ten years, depending on technological advancements and the partner’s needs.
Both Tetra Pak and SIG are top global companies in paper packaging for the F&B industry: in 2023, Tetra Pak achieved a revenue of EUR 12.7 billion, selling 179 billion paper boxes worldwide; SIG generated a revenue of EUR 3.21 billion, with a net profit of approximately EUR 318 million, and produced 50 billion paper boxes.
“The challenges of becoming a high-tech paper packaging supplier for the F&B industry, specifically the dairy and beverage industry, are significant, not only in Vietnam but also in Southeast Asia. Currently, about five FDI companies dominate this market in Vietnam.
While we are not in a position to discuss FDI issues at this time, we are delighted to partner with Vietnamese companies to introduce new products to the market, such as with Vinamilk, TH True Milk, Nutifood, and IDP,” said Ms. Vo Xuan Minh Kha.
Vietnamese packaging companies primarily produce carton boxes, paper boxes for technological equipment, or ‘ready-to-eat’ paper boxes in the F&B industry, which do not require advanced technology or stringent quality standards like sterilization. Thus, the potential of the aforementioned paper packaging industry remains in the hands of FDI companies, with Tetra Pak and SIG leading the way.
Is SIG aiming for a new boost in the Vietnamese market?
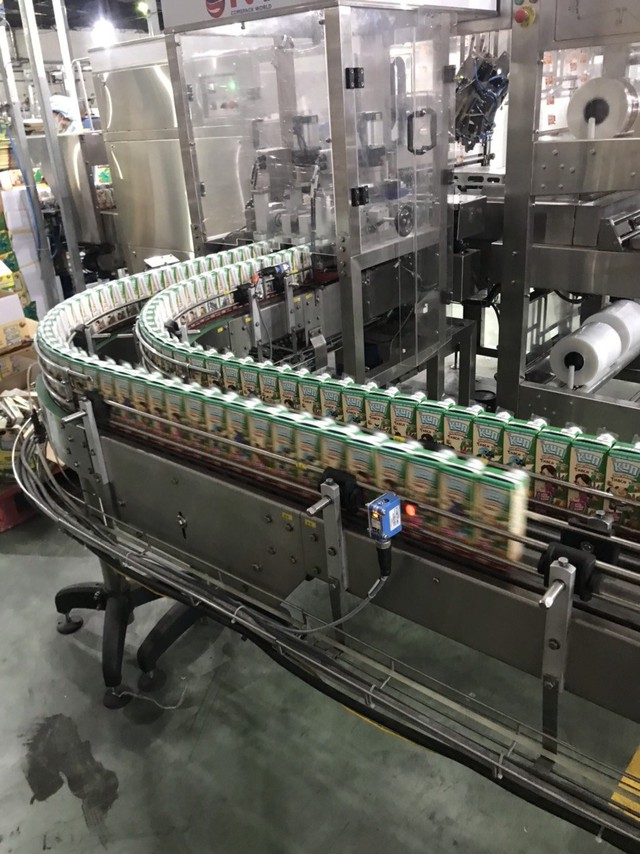

A filling line provided by SIG to a customer in Vietnam.
“SIG is intensifying its media dialogues to highlight positive developments and seize opportunities presented by Vietnam’s rapidly growing market. In 2024, consumer spending in Vietnam is driven by robust economic growth, resulting in increased disposable income as the impact of the pandemic fades.
Vietnam has always been a strategically important market for SIG in the region due to its vast potential and supportive government regulations to promote sustainability. The packaging industry in Vietnam is one of the fastest-growing industries, with an expected growth rate of 15% to 20% in the coming years.
Data from Mordor Intelligence Inc., a leading market research organization, shows that the scale of Vietnam’s paper box packaging market is estimated at USD 2.6 billion in 2024 and is projected to reach USD 4.14 billion in 2029, growing at a CAGR of 9.73% during 2024-2029. SIG aims to strengthen its presence to capture the opportunities presented by this growth.
The packaging industry is undergoing significant changes, with an increasing focus on sustainability and innovation. We aim to leverage our R&D capabilities to drive innovations in the industry. Our flexible packaging solutions enable customers to effectively navigate economic fluctuations.
We also strive to minimize our CO2 footprint at every stage of the value chain, from using certified raw materials to production, packaging, usage, and recycling. Our solid foundation affirms SIG’s leading position in providing sterile packaging solutions,” explained Ms. Vo Xuan Minh Kha on her first appearance in the media.
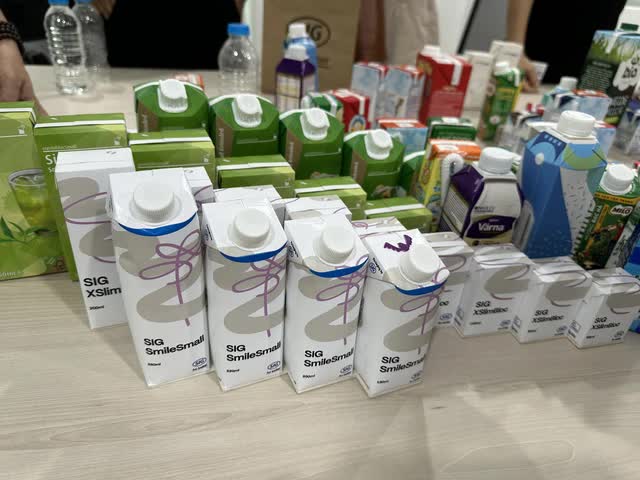
Flexibility and efficiency are two of the key criteria that SIG prioritizes in its development journey.
According to Ms. Kha, the opportunities and growth potential in Vietnam’s packaging industry are immense, and they welcome competition.
SIG’s key advantage is that their packaging ensures the safe delivery of affordable and stable nutrients under normal storage conditions, with the lowest carbon emissions compared to other packaging types. SIG is also a leader in striving for fully renewable packaging systems.
Firstly, SIG’s technology offers unmatched flexibility: they are industry leaders in volume, format, design, and unique product flexibility. One of their filling machines for single-portion paper boxes can handle up to nine volumes (80ml-200ml) on the same system, allowing customers to seize market opportunities while maintaining affordability.
Secondly, SIG is committed to sustainability goals: to rapidly expand sustainable packaging options with lower CO2 emissions, we need innovations in packaging that reduce CO2 and can be applied to pre-installed filling machines. SIG can deliver on both fronts.
The SIG Terra product line offers a range of innovative, more sustainable, and lower-carbon packaging options. SIG aims to achieve 90% paper content in its paper boxes by 2030, ensuring complete recyclability worldwide.
Thirdly, SIG’s filling machines are highly efficient, with the lowest wastage rates in the industry, starting at just 0.5%.
Lastly, SIG has five R&D centers worldwide: the Group works closely with customers to develop innovative packaging solutions that meet their diverse needs. The R&D center for Asia-Pacific is located in Suzhou, China.
These centers also enable SIG to assist customers in developing formulas and conducting trials, helping them accelerate innovation and bring products to market in the shortest possible time.