According to Nikkei, Toyota Motor will install a giant casting machine at a plant in Japan this year. The aim is to reduce electric vehicle production costs by adopting Tesla’s advanced techniques.
Located at the Aichi production hub, this will be one of Japan’s largest casting machines with a clamping pressure of 9,000 tons. By casting multiple parts together in one step, the EV manufacturer can reduce vehicle weight and improve production efficiency.
Japanese company Ube Machinery is the manufacturer of this super-large casting equipment. The machine will be 10 meters wide, 22 meters long, and about 7 meters high, covering an area the size of a tennis court.
Toyota plans to apply gigacasting technology to its next-generation EV, the LF-ZC, launching in 2026 under the Lexus brand. The vehicle body will be divided into three parts: front, middle, and rear. The front and rear sections will be produced using gigacasting.
Gigacasting technology is expected to be used for prototyping EV components rather than mass production. Toyota will evaluate whether this technology leads to a reduction in parts and processes.
Over 10 companies are adopting gigacasting technology, mostly in the US, Europe, and China. Tesla utilizes gigapress machines with clamping pressures ranging from 6,000 to 9,000 tons.
Honda Motor has unveiled a 6,000-ton machine at an R&D facility in Tochigi Prefecture to prepare for mass production. Nissan Motor also plans to install a 6,000-ton machine in fiscal 2027, aiming to reduce component weight by 20%.
Previously, in an interview, CEO Koji Sato stated that Toyota would prioritize “BEV (battery electric vehicle) thinking,” along with a drastic change in its business approach – from production to sales and services. The ultimate goal is to realize the carbon neutrality plan set by his predecessor, Akio Toyoda.
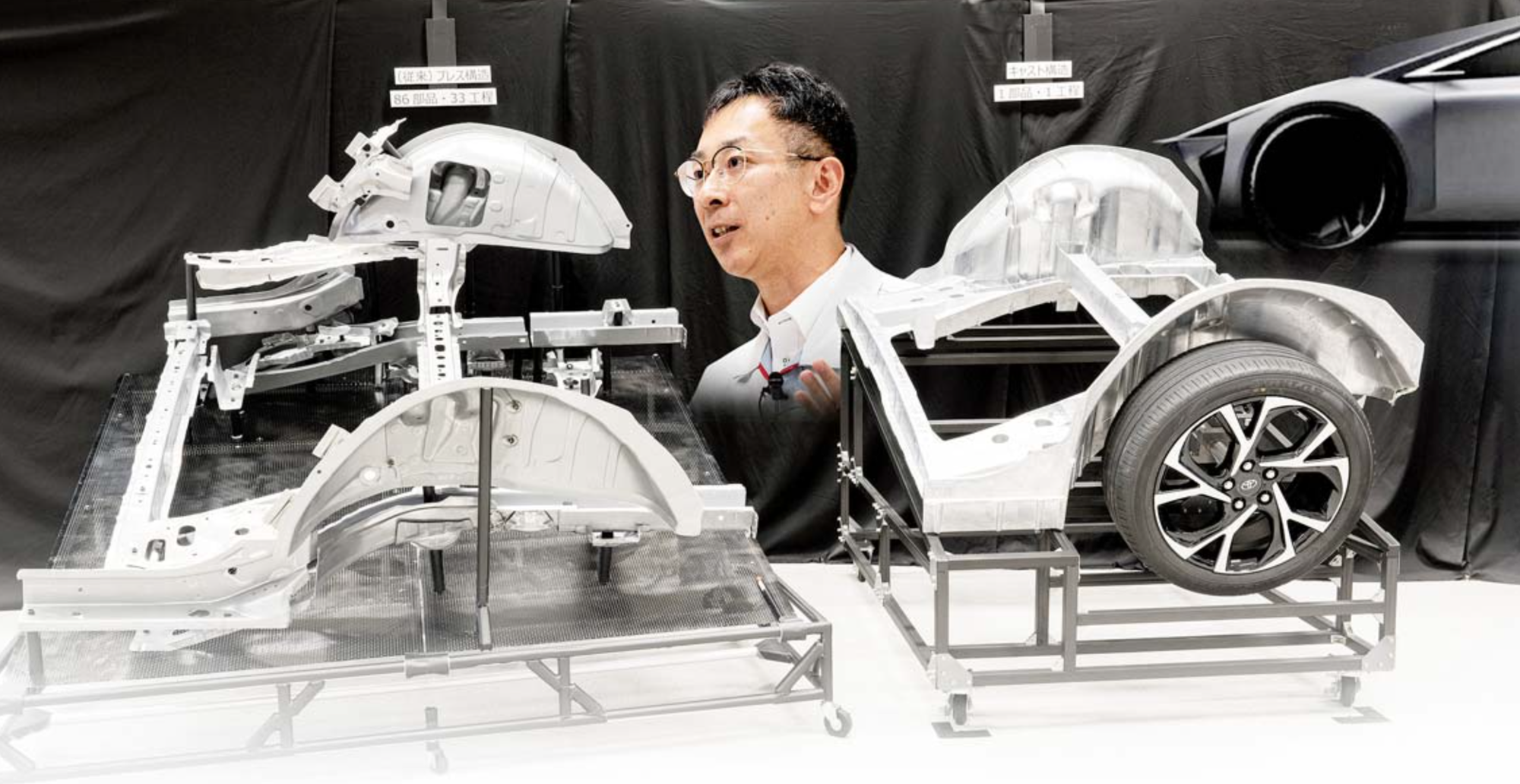
“Toyota is doing a lot of things that no one expects. We are creating diversity to meet consumer needs,” said Simon Humphries, a Toyota executive.
Mr. Sato also established an organization called the “BEV Factory” to break down Toyota’s traditional approach to development and production. “This is an extremely good result that far exceeded expectations. The auto market is recovering rapidly after three years of being affected by the pandemic and the chip supply crisis,” said Christopher Richter, an analyst at CLSA Securities Japan, about Toyota.
Gigacasting, a modern aluminum casting technology, is predicted to set a new standard for vehicle manufacturing. This method was adopted by Tesla for its Model Y line in 2020. Previously, the main body of a car would be constructed by welding or stamping a large number of separate parts together, whereas gigacasting or megacasting involves pumping molten metal into a mold and filling it under high pressure before cooling.
With this technology, Tesla has cut related costs by up to 40%. The weight of the rear body of the Model Y has also been reduced by 30%.
“Megacasting is the perfect example of being able to replace 100 parts with just one. This saves time, labor, cost, and factory space, replacing multiple welding robots with a single machine. Producing a car will be much faster,” said Erik Severinson, head of strategy at Volvo Cars.
Toyota is researching similar techniques to ramp up large-scale electric vehicle production. During a series of plant tours, executives acknowledged that there is much to learn from Tesla and other Chinese EV manufacturers.
“To be honest, we are late to the game with gigacasting. However, the group believes that we can create a product that is cheaper, lighter, and thinner with high performance,” said Kazuaki Shingo, Toyota’s head of production.
Source: Nikkei Asia, Financial Times
Which car brand sells the most urban SUVs in Vietnam?
The title for the top spot in the compact SUV segment in Vietnam does not belong to Toyota or Hyundai, but rather another brand.
Vietnamese Car Manufacturer Quietly Developing Small Electric Vehicle Platform, Taking on Tesla and Chinese Car Companies at a Lower Price
The CEO of Ford revealed that the company is currently working on a specialized platform for affordable electric vehicles.