At the recent annual general meeting of shareholders, DRC – one of the veterans of Vietnam’s rubber industry – officially unveiled its plans to develop a specialized tire line for electric vehicles in direct collaboration with VinFast. According to DRC, this project has entered the final stages of development and is expected to be commercialized by June this year.
This strategic move by DRC aims to capitalize on the global automotive industry’s shift towards electrification while showcasing Vietnamese enterprises’ efforts to master automotive manufacturing technologies.
A Half-Century of Experience
Established in 1975, DRC is a member of Vietnam Chemical Group (Vinachem) and is recognized as one of Vietnam’s leading tire manufacturers. With its main factory located in Hoa Khanh Industrial Zone, Da Nang, DRC has thrived in both domestic and international markets. The company offers a diverse range of tires for motorcycles, trucks, buses, and passenger cars.
Notably, DRC’s DriveForce brand has been exported to several countries, including the US, Brazil, and Myanmar, and has earned international certifications such as DOT (US) and E-Mark (Europe). With a radial tire production capacity of up to 1 million units per year, DRC not only holds a strong position in the domestic market but also has the potential to become a significant player in the Southeast Asian electric vehicle supply chain.
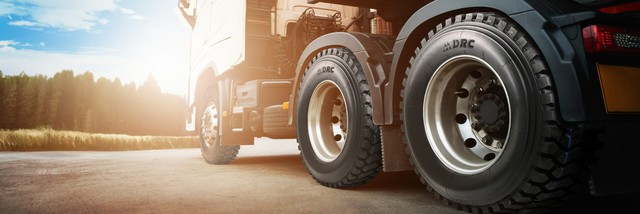
DRC was established in late 1975.
On April 25, 2025, at the annual general meeting of shareholders, DRC officially announced its plans to develop a tire line for VinFast’s electric vehicles. This collaboration between Vinachem and VinFast aims to bring Vietnamese-branded tires to premium electric models like the VF 8 and VF 9.
This partnership goes beyond mere product supply; it is a strategic step towards localizing the electric vehicle supply chain in Vietnam. With over 50 years of experience in the rubber industry, DRC will undertake the research and development of electric vehicle tires that meet VinFast’s stringent technical standards.
The Electric Vehicle Tire Conundrum
While automotive tires have been around for a long time, tires for electric vehicles present significant differences due to the stringent requirements of 21st-century transportation.
Manufacturing tires for electric vehicles is considered a technological challenge, necessitating a redefinition of the entire design and material selection process.
Here are the reasons why producing tires for electric vehicles is more complex than producing conventional tires:
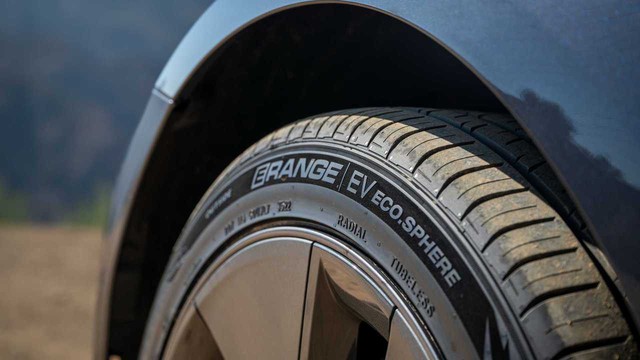
Electric vehicle tires have distinct characteristics that require more advanced production techniques.
1. Higher Load Capacity
Electric vehicles have larger battery packs located under the floor, increasing the overall weight by 200 to 500 kg compared to gasoline-powered vehicles in the same segment. This requires tires with superior structural strength, from the casing to the sidewalls and protective layers, to withstand the additional load.
The commonly used materials for EV tire carcasses are aramid or high-grade steel, which offer high strength while maintaining lightweight properties. Without proper reinforcement, the tires may deform, increasing the risk of tire bursts or uneven wear.
2. Superior Traction
Unlike gasoline engines that take time to reach optimal power output, electric motors deliver peak torque instantly when the accelerator is pressed. This demands exceptional traction from the tires, especially during sudden acceleration. Additionally, the tires need to provide sufficient braking force to stop the heavier vehicle.
Manufacturers of electric vehicle tires must use materials with just the right amount of softness to provide good traction without compromising durability. The tread pattern design also needs to be optimized to increase friction while reducing the risk of skidding on wet roads.
3. Reduced Noise
As electric vehicles operate almost silently, any noise becomes more noticeable, including that generated by the tires during rolling. To address this issue, electric vehicle tires often incorporate a foam insert and specific sidewall design to dampen sound waves.
Integrating the foam layer without affecting the tire’s balance and temperature is a challenging technology that requires precise assembly and testing procedures.
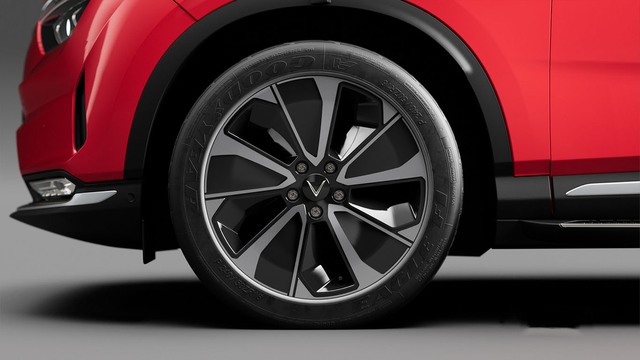
Illustration.
4. Low Rolling Resistance
One of the most critical factors for electric vehicles is maximizing the range on a single charge. Electric vehicle tires must be designed to optimize rolling resistance, which directly impacts energy consumption.
To achieve this, the tire structure must reduce friction with the road surface without compromising traction. The rubber compound used should have the ability to “recover from deformation” quickly. This is a challenging chemical and physical problem that not all companies can solve.
5. Longevity
Despite experiencing higher friction and load, electric vehicle tires must match or exceed the longevity of traditional tires to ensure economic efficiency for users. This demands superior resistance to wear, heat, and deformation.
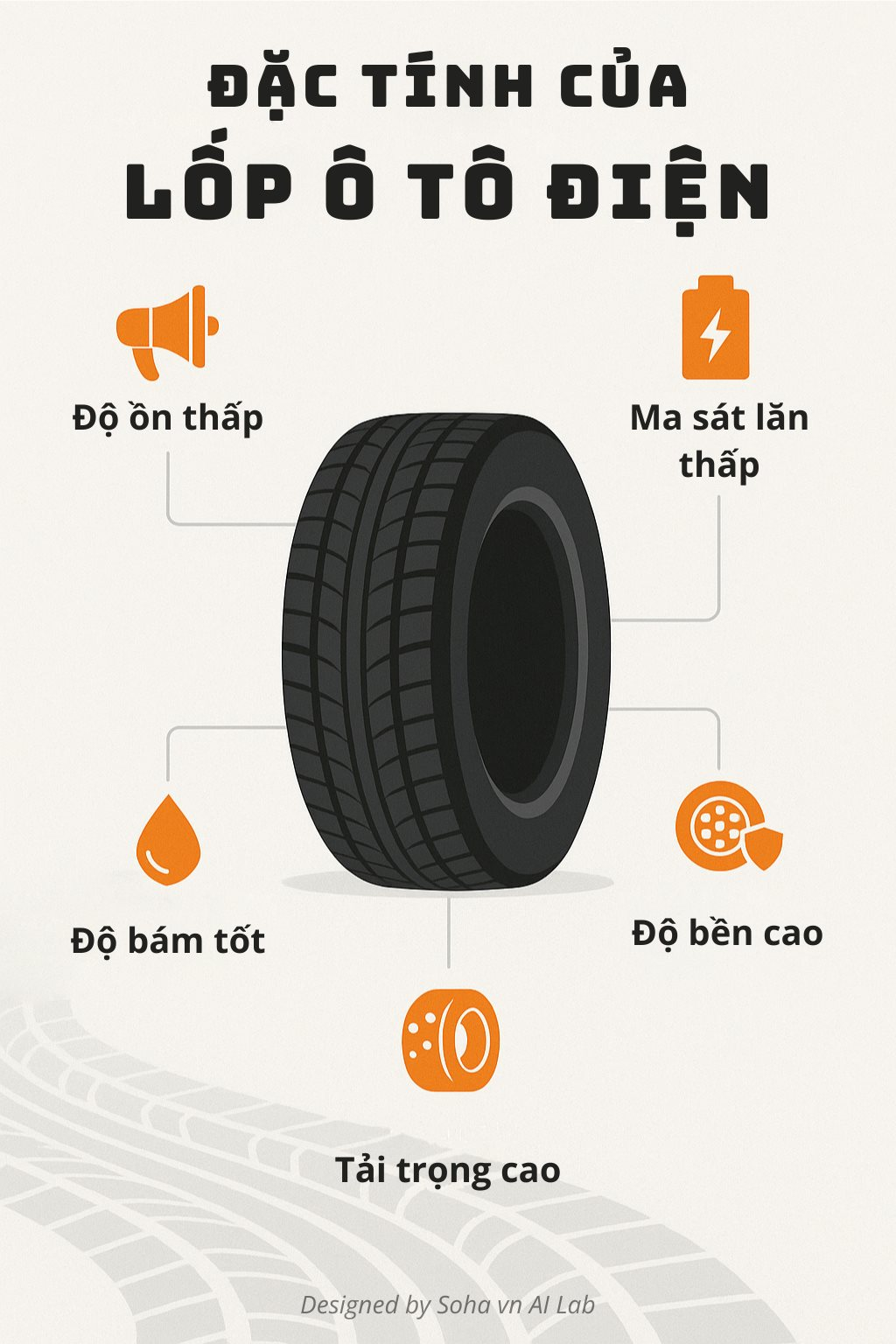
A Nearly 20-Year-Old Lexus ES is Priced at Over 400 Million: With 140,000 km on the Clock, This Timeless Car Has a Well-Preserved Interior and an Exterior that Reflects the Passage of Time.
In 2008, the Lexus ES 350 was a rare sight on the roads, and its presence always turned heads. Its sleek and sophisticated design, coupled with its hefty price tag, made it a true luxury car that stood out from the crowd.
The Unavoidable Excise Tax on Gasoline
“According to the Minister of Finance, continuously encouraging and exempting gasoline from taxation will make it very challenging to alter behavioral patterns.”