Amid an increasingly crowded market for low-cost cars from China, G-Tekt (a parts supplier for Honda) has teamed up with world-leading steelmaker ArcelorMittal to manufacture car body frames at a lower cost for electric vehicles.
Under the alliance, G-Tekt will license technology from ArcelorMittal, which will then be used to produce EV chassis components by consolidating 5-10 parts into a single seamless metal casting.
G-Tekt’s new manufacturing method closely mirrors Tesla’s gigacasting process, but instead of aluminum alloys, G-Tekt will use a variety of steel grades, which are cheaper to produce.
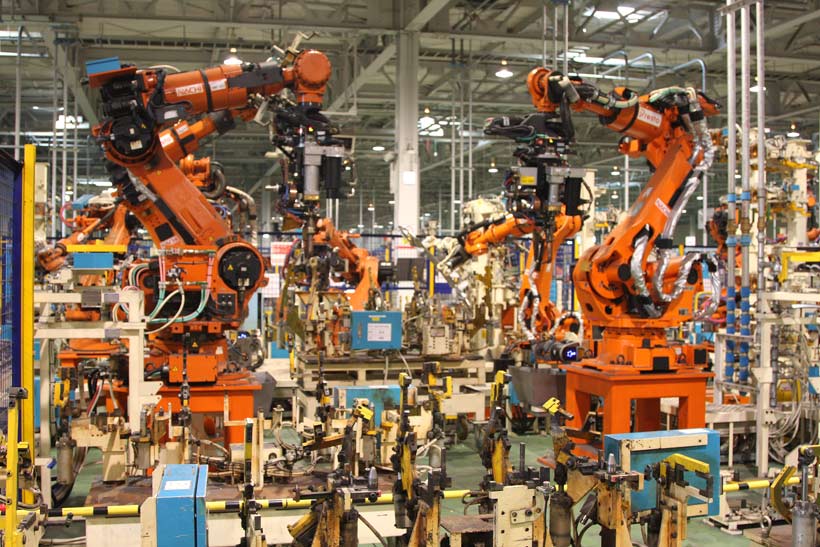
Inside G-Tekt’s plant in the Netherlands. Photo: G-Tekt
G-Tekt plans to begin using the manufacturing process in 2028 or later and will be proposing it to its automotive partners, which include Japanese automakers such as Honda. When implemented, the process could reduce the cost of producing automotive body parts by around 20% compared to gigacasting.
This comes as Chinese EV manufacturers have gained a price advantage. In China, BYD, the country’s largest EV maker, has been able to produce vehicles at extremely low costs, with one model costing only around $6,500 (165.5 million VND).
The inexpensive Chinese EVs are not only impacting the domestic market but also the global market. Most recently, Tesla made the decision to lay off around 10% of its workforce worldwide.
GIGACASTING: A NEW TREND IN AUTOMOTIVE MANUFACTURING
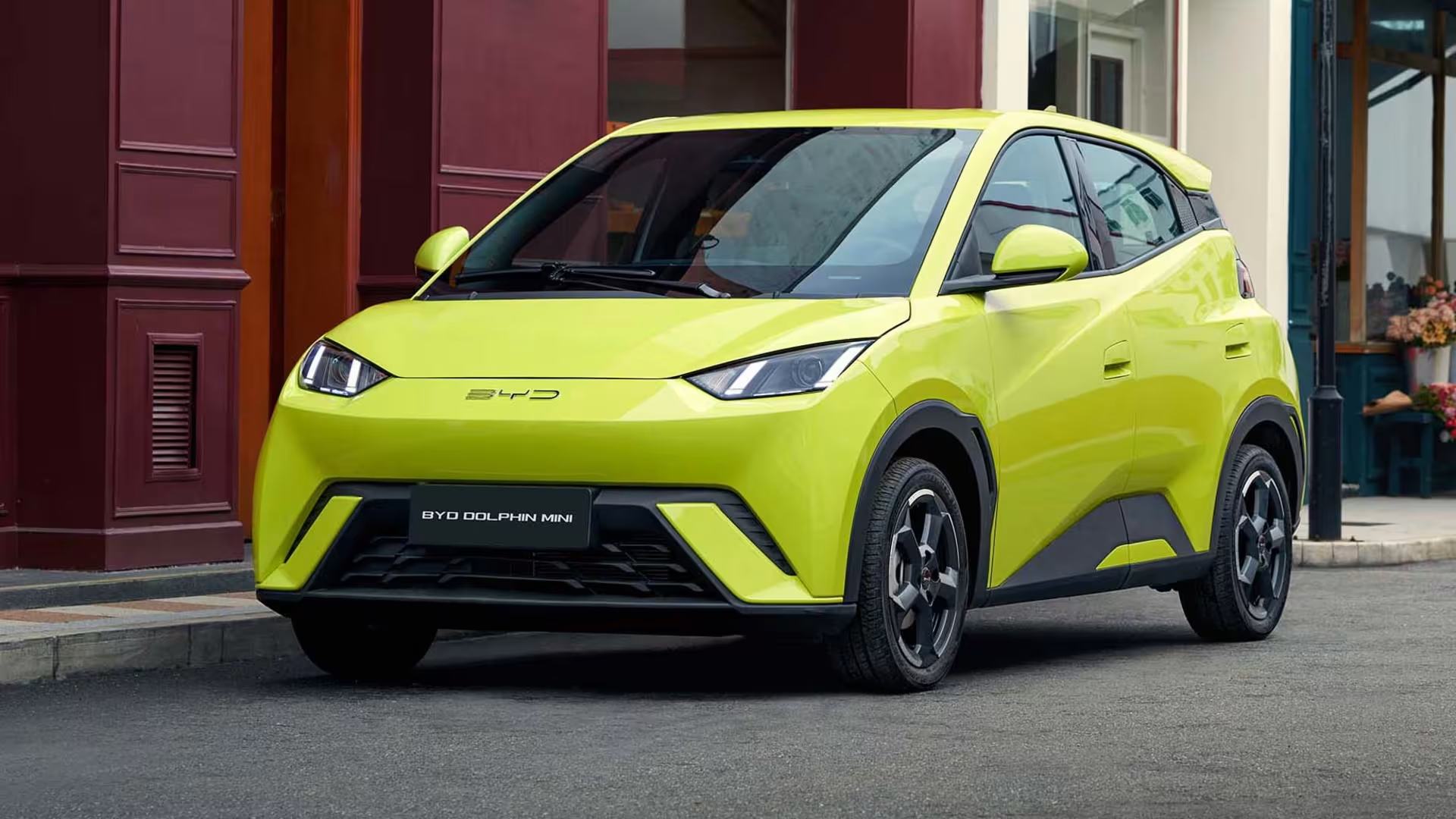
The Dolphin Mini is the cheapest model from BYD.
Gigacasting is a process pioneered by Tesla. The method has been seen as a way for EV manufacturers to increase their production efficiency.
Due to its advantages of cutting production costs and producing stronger, stiffer vehicles, many manufacturers around the world have adopted the practice. In China, Xpeng and Zeekr (owned by Geely) are using gigacasting to reduce vehicle weight and manufacturing costs.
Toyota is also adopting gigacasting in its own way, planning to use it in the production of its dedicated electric vehicle models scheduled to launch from 2026.
Meanwhile, Nissan will adopt gigacasting for some electric vehicle models in fiscal 2027 and is aiming to reduce body material costs by approximately 10%.
While gigacasting is a relatively new manufacturing method, some have criticized Japanese manufacturers for being behind in adopting the practice when it comes to using steel instead of aluminum alloys. However, Japanese manufacturers seem to be struggling to master the technology.
Technically, the steel parts will be galvanized to prevent rust. However, areas where the steel will be welded cannot be galvanized, as the zinc coating will cause the welds to have a poor bond.
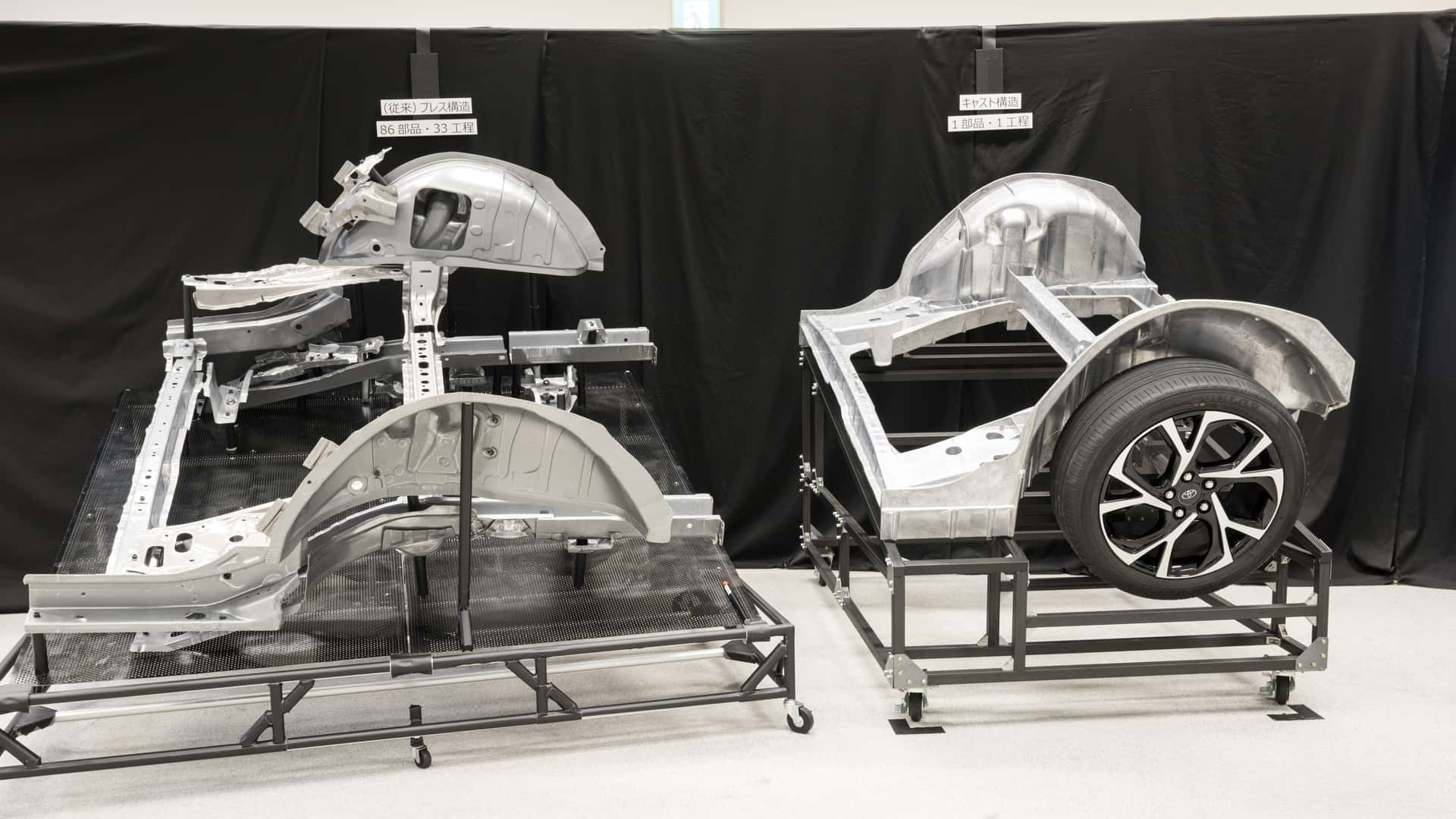
The rear frame of a Toyota vehicle using gigacasting (right) consists of only one part and takes 1 production step, while the conventional manufacturing method (left) requires 86 parts and 33 steps.
G-Tekt, using technology from ArcelorMittal, will use lasers to weld the steel components into one seamless part. The initial cost of implementing the technology is expected to be relatively low, as G-Tekt will be able to use existing equipment.
Currently, batteries and the vehicle body are two major factors that determine a vehicle’s competitiveness in terms of price. While batteries can account for up to 30% of an EV’s cost, the materials used to make the vehicle body can account for around 10%.
By implementing the new process, G-Tekt could cut a few percentage points from the overall cost of producing an electric vehicle.